Hola de nuevo compañeros, aquí sigo aunque no lo parezca, y con un trabajo que quiero compartir con vosotros. También felicitar a Namberguan por su obra, estoy seguro que ambos sentimos lo mismo cada vez que empuñamos un filo hecho por uno mismo ahora que lo hemos probado.
Llevo ya muchos años picado con hacerme un cuchillo y al final me he arrancado a hacerlo, y si, el programa de "forjado a fuego" me ha ayudado a darme el animo, de el he aprendido bastante junto a lectura masiva en internet de gente que comparte su experiencia.
Lo primero que necesitaba era una lijadora de banda, y las opciones son pocas: o te compras una buena y por lo tanto cara (mucho), te compras una barata y te das cuenta de que es una mierda y acabas comprándote la cara, o te la haces casera como es mi caso y el de muchos otros, salvo por la diferencia de que ves cada montaje "casero" que alucinas, y la mía no me acuerdo exactamente pero me habrá salido el material en unos 50€. Dicen que a los hijos feos se les quiere igual, esto debe ser parecido. Debo decir que no he sacado fotos del paso a paso de casi nada, me he liado a hacer y sacaba fotos conforme me acordaba.
Antes de que lloréis sangre explico un poco de que esta hecho este monstruo de frankenstein. El motor lo he comprado de segunda mano y tendrá mas años que algunos de nosotros juntos, pero funciona bien, solo que es trifasico y tengo que engañar la tercera fase con condensadores ya que uso monofasica, funciona pero a veces no arranca bien y hay que darle un empujoncito a la lija para que arranque, nada grave, una vez en marcha tiene mucha fuerza y no lo paras. La polea motriz es una rueda de carretilla que por diámetro y revoluciones del motor me da una velocidad de lija buena, hice el calculo en su momento paro no me acuerdo. el agujero del eje es mas pequeño que el del motor así que tuve que agrandarlo haciendo una broca casera (como no...) y también tuve que equilibrarla ya que este tipo de ruedas están hechas para rodar a 5km/h y ni se molestan es que estén bien hechas, y a 1400rpm era exagerado lo que botaba el motor. Mirando la rueda de frente gira a izquierdas para que la parte superior que es donde trabajo me aleje las chispas. Los rodillos son recuperados de cuando cambio algún kit de distribución de motor de coche, y el resto de hierros retales que me encuentro por ahí (donación generosa de mi jefe). Las bandas de lija son de aliexpress, de medida 2"x72" o igual a 50mm x 1800mm, salen tiradas de precio aunque no sean muy buenas y el tipo de unión no es el mas adecuado pero sirve y se puede solucionar fácilmente.
Una vez probada y ver que va todo bien hay que dejarla aseada dentro de lo que se puede. Por supuesto con sobras que tengo por ahi de botes de spray, y un interruptor (donación generosa de mi padre) Ahora he puesto un trozo de granito recortado a medida arriba que va a ser donde trabaje los planos que se sujeta con imanes y una plancha de hierro pegada para mover o quitar si me interesa (donación generosa de una reforma en el patio de al lado del taller).
Ahora ya puedo empezar a hacer cositas. Lo primero comprar carne para echar a las brasas. El acero lo he comprado en la tienda "suministros para cuchillos" por si a alguien le interesa, acero D2, 52100 y 9260, no diré cantidades ni a que van destinados, sorpresa.
Yo que soy masoca empiezo por el menos indicado para empezar, el D2, un trozo de 4mm x 40mm x 260mm, buscando hacer un utilitario principalmente desollador, por eso ese acero para que aguante el filo y la corrosión aun sin llegar a ser inoxidable.
Ya he dicho que no he sacado fotos de todo así que aquí lo pongo prácticamente acabado.
En esta ultima se nota que se me ha ido la mano, es lo que tiene ser diestro. Hice un intento de templar haciendo un horno con ladrillo refractario y dos sopletes de fontanero que sin ni acercarse a lo adecuado aun pude tras mucho rato ponerlo al rojo cereza y meterlo en aceite usado de coche, se templo pero no como debiera, los ladrillos refractarios soportan mucha temperatura pero no son aislantes y se pierde mucho calor, aun así algo de dureza tenia.
Lo que me lleva al siguiente paso, la fragua.
Para la fragua hay varias opciones, que yo conozca: de carbón, de gas y eléctricas. Al principio valore el carbón (mineral), por ser económico, pero es una guarreria entre sacos, residuos, olores, humos, así que fuera. El eléctrico ni me lo plantee, y elegí el gas, mucho mas limpio. Para hacerlo como he dicho el ladrillo refractario es una mala opción pues pierdes mucho calor, hay que usar ladrillo cerámico aislante. Por tema precio me quede los T23 (recomiendan mas los T26 que aguantan un poco mas pero salen mas caros y tampoco hay demasiada diferencia) y para pegarlos mortero refractario. No sabéis que tortura echar el mortero en esos ladrillo, son tan porosos que conforme les toca la pasta absorbe el agua y la seca, tuve que desarmarlo entero y sumergiendo los ladrillos en agua ya puedes trabajar bien con la pasta. Hay que dejar el mínimo espacio entre cada ladrillo o sera un punto de fuga de calor. Como refuerzo una jaula metálica ya que estos ladrillos son muy frágiles (con la uña podrías cortaros) y los quemadores son unos tubos de escape de coche y un engendro de valvulas y tubo de cobre acabado en unas boquillas de 0,7mm y la válvula que se acopla a la bombona de alto caudal. De momento estoy usando butano hasta que pille propano para probar. Los quemadores por supuesto super calculados según ecuaciones de la nasa sacadas de becarios yonquis, vamos, a ojo "y a ver que sale". Mide 70cm de larga con idea de hacer cositas... largas.
A funcionar bonita. Aquí tengo un quemador a tope y el otro a mitad. Que el tubo se caliente a mitad es claramente un fallo de diseño por medidas o lo que sea que tengo que averiguar y solucionar ya que creo que no me alcanza toda la temperatura que debiera y creo que puede ser por eso. Raro seria que saliera todo bien a la primera haciendo a ojo lo que te sale de las narices.
Para volver a templar el cuchillo he probado a hacer un templado diferencial con mortero refractario, aunque por lo leído es muy difícil hacer un templado diferencial en acero D2 ya que es de muy alta templabilidad (facilidad de coger temple), tanta que templa al aire, pero mis cojones por delante.
Para mayor efectividad del proceso he sumergido solo el filo en aceite de manera horizontal, dejando el lomo al aire para que con la capa de mortero al rojo se enfríe mas lentamente. Menuda liada de humo y fuego del aceite.
El cuchillo pilla un color negro que aun con lijadora de banda cuesta quitar.
Ahora toca el mango, y como comente en un post anterior sera de micarta casera. He usado cincha de tela de algodón ya que con la de poliester/nylon no queda nada bien y de epoxi Zap E-poxi de 30min, sale mas barato que el araldite.
Aquí unas pruebas con distintas telas.
Al final elijo un mango de capas verde y marrón (que por algún motivo parece que se ha transformado a negro), con una capa beige que quedara en el centro del mango. Vale la pena usar tela de cierto grosor por que con tela fina tipo trapo acabas loco de poner una capa tras otra.
Y por fin aquí el resultado mi primera criatura:
Para unir el mango a la hoja he usado tubo de latón de 8mm aparte de epoxi, dudo mucho que se suelte. El mango tiene un acabado superficial de cianocrilato como ya explique en otro post, resalta los colores de las telas, las protege, y según quieras te deja un acabado rugoso de alto agarre o pulido a espejo. En esta foto sale con el vaciado oscuro del templado en aceite, al principio lo deje así por que hacia un contraste bonito aunque no se vea mucho en la foto, pero frotando dejaba residuo y eso trabajando carne no es bueno y ahora esta todo el acero pulido, por supuesto afilado hasta afeitar.
Mas adelante le haré una funda, de momento lleva una donada de otro cuchillo.
Y como siempre, espero que os guste.
Y eso si....
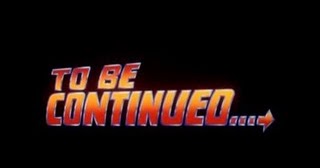